A Catalyst Revolution: Green Hydrogen and Acetic Acid from Ethanol
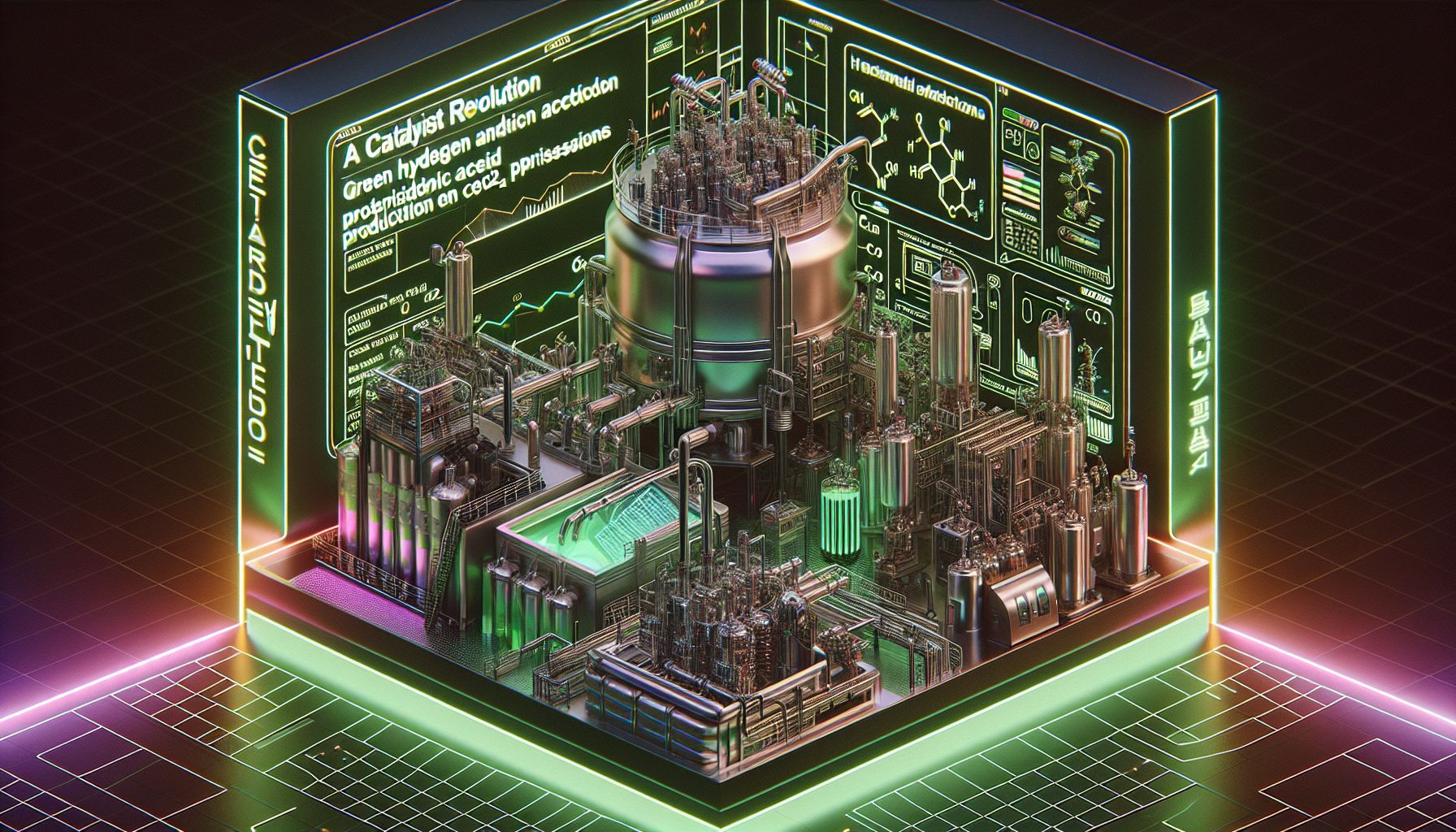
London, Friday, 21 February 2025.
Researchers unveil a groundbreaking catalyst to produce hydrogen and acetic acid from ethanol without CO2 emissions. Could this eco-friendly method give traditional production processes a run for their money? Stay tuned!
A Game-Changing Discovery
I’m excited to share news of a remarkable breakthrough that just emerged yesterday. Scientists from Peking University and Cardiff University have developed a novel catalyst that transforms ethanol into hydrogen and acetic acid without releasing CO2 directly into the atmosphere [1][2]. What makes this particularly fascinating is how the catalyst operates at just 270°C [1], significantly cooler than traditional hydrogen production methods that require heating natural gas to a scorching 1000°C while emitting 9-12 kg of CO2 per kg of hydrogen [2].
The Technical Magic
The secret lies in the catalyst’s clever design, which uses molybdenum carbide enhanced with platinum and iridium [1]. Through my analysis of the data, I can tell you that this isn’t just marginally effective - it achieves an impressive 84.5% selectivity for acetic acid production [1]. Professor Ding Ma, the lead researcher, explains that while similar reactions have been attempted before, achieving such high selectivity toward acetic acid was previously impossible [1].
Economic Reality Check
Now, I should be transparent about the economic challenges. As Fabio Ribeiro from Purdue University points out, there’s currently a gap between production costs and market value - the combined value of the hydrogen and acetic acid produced doesn’t yet exceed the cost of the ethanol and process water used [1]. However, Ma notes that global prices for ethanol and acetic acid can fluctuate significantly [1], which could make this process more economically viable under the right market conditions.
Future Prospects
Looking ahead, there’s still work to be done. The researchers are exploring ways to reduce costly iridium usage or replace these precious metals entirely [1]. While water electrolysis remains a leading method for hydrogen production, Ma suggests this new approach could be particularly valuable for distributed, small-scale manufacturing [1]. With the chemical industry consuming roughly 100 million tonnes of hydrogen annually [1], and global acetic acid demand exceeding 15 million metric tons per year [2], the potential impact of this technology is significant.